Revolutionizing the Industry: Advances in Hydraulic Shearing Machines
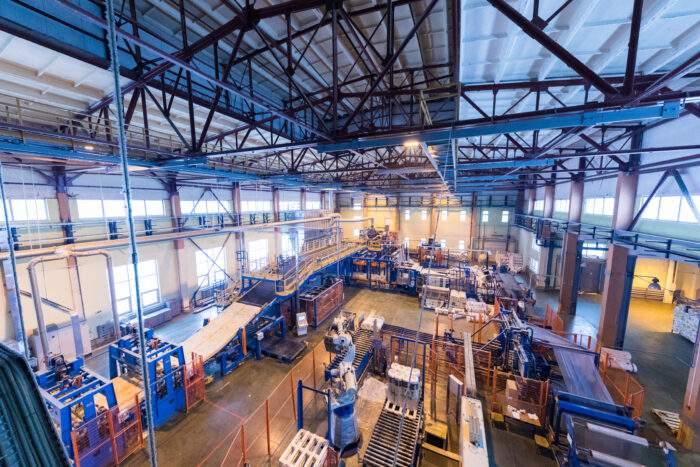
Introduction
In the dynamic world of manufacturing and metalworking, technological advancements often act as the driving force behind industry transformation. A prime example of such a transformation can be witnessed in the realm of hydraulic shearing machine. Once deemed as basic tools for cutting metal sheets, hydraulic shearing machines have undergone a remarkable evolution that has left an indelible mark on the manufacturing landscape. In this comprehensive blog, we delve deeper into the revolutionary advances that have propelled hydraulic shearing machines into a new era of efficiency and precision.
Understanding the different types of metal shears, from guillotine shears to rotary shears, is crucial for selecting the right tool to achieve precise and efficient metal cutting in various industrial applications
The Conventional Role of Hydraulic Shearing Machines
Historically, hydraulic shearing machines have played an indispensable role in metal fabrication by providing a means to accurately cut metal sheets and plates. However, the process often involved manual intervention, limiting the speed and accuracy of production. This traditional approach, while effective, lacked the finesse needed to keep up with the demands of modern manufacturing.
Emergence of Technological Breakthroughs
The transformation of hydraulic shearing machines from rudimentary tools to technological marvels has been driven by a series of breakthroughs:
- CNC Integration: The integration of Computer Numerical Control (CNC) technology has revolutionized the operation of hydraulic shearing machines. The transition from manual adjustments to automated precision cutting has not only improved accuracy but also accelerated production timelines. CNC technology has ushered in a new era where complex designs can be executed with unparalleled precision.
- Intuitive Touchscreen Interfaces: The era of clunky buttons and switches has given way to intuitive touchscreen interfaces. These user-friendly panels empower operators to input cutting parameters, angles, and dimensions with ease. The graphical representation of the cutting process enhances the overall user experience and minimizes the learning curve for new operators.
- Automated Material Handling: The inclusion of automated material handling systems has streamlined the manufacturing process. These systems efficiently feed metal sheets into the machine, align them accurately, and remove finished pieces. By reducing downtime between cuts, manufacturers can optimize production workflows.
- Real-time Monitoring and Visualization: Cutting-edge hydraulic shearing machines are equipped with sensors and cameras that provide real-time monitoring of the cutting process. Operators can remotely observe the operation, promptly address potential issues, and make real-time adjustments. This level of visibility enhances both safety and efficiency.
- Predictive Maintenance through IoT: The Internet of Things (IoT) has facilitated the implementation of predictive maintenance strategies. Modern hydraulic shearing machines can monitor their own performance, detecting signs of wear and tear and generating maintenance alerts. This proactive approach prevents unexpected downtime and prolongs the lifespan of the machines.
Benefits and Far-reaching Impacts
The advancements in hydraulic shearing machines have brought about transformative benefits across industries:
- Skyrocketing Productivity: The amalgamation of CNC technology, automation, and real-time monitoring has catapulted productivity to new heights. Manufacturers can now produce accurately cut pieces in significantly less time, enabling them to meet market demands with unprecedented efficiency.
- Unsurpassed Precision: CNC-controlled machines offer precision that was once inconceivable. This precision not only minimizes material wastage but also ensures consistency in quality across batches.
- Optimized Labor Utilization: Automation’s takeover of manual tasks allows skilled operators to focus on critical aspects of the production process. This results in enhanced labour efficiency and the deployment of human resources where they matter most.
- Diverse Applications Unleashed: The versatility of modern hydraulic shearing machines has expanded the scope of possibilities. From intricate patterns to complex metal designs, these machines cater to a diverse array of industry needs.
- Cost-effectiveness in the Long Run: Although the initial investment in advanced hydraulic shearing machines might be higher, the long-term advantages in the form of elevated productivity, minimized material wastage, and reduced downtime translate into substantial cost savings.
Conclusion
The evolution of hydraulic shearing machines encapsulates the dynamic nature of the manufacturing landscape. We also manufacture ironworker machine. The infusion of CNC technology, automative, real-time monitoring, and predictive maintenance has unlocked unprecedented potential within these machines. The introduction of automated CNC technology has revolutionized the precision and efficiency of sheet metal bending machine in the manufacturing process. As industries continue to demand superior quality, faster production, and heightened efficiency, the progressive strides in hydraulic shearing machines are poised to reshape the very essence of metalworking. Manufacturers who embrace these groundbreaking innovations are not merely adapting; they are positioning themselves as pioneers in a future marked by manufacturing excellence. The integration of CNC technology, automation, real-time monitoring, and predictive maintenance has revolutionized the capabilities of these machines. As industries continue to demand higher quality, faster production, and greater efficiency, the advancements in hydraulic shearing machines are poised to reshape the metalworking sector for years to come. Manufacturers who embrace these innovations are well-positioned to thrive in the competitive manufacturing landscape of the future.